PCB沉金工艺流程简介前处理
- 发布时间:2025-05-23 15:57:06
- 浏览量:350
PCB沉金(化学镀镍浸金,ENIG)工艺中的前处理是确保后续金属沉积质量的关键步骤,直接影响镀层的结合力、平整性和耐腐蚀性。以下为前处理流程的详细介绍及注意事项:
1. 除油(Degreasing)
-
目的:去除铜箔表面的油脂、指纹、灰尘及有机污染物,确保铜面洁净。
-
方法:
-
使用酸性或碱性除油剂(如碱性脱脂液),通过化学浸泡或喷淋方式处理。
-
温度通常控制在40-60℃,时间约3-5分钟。
-
-
关键点:
-
若除油不彻底,会导致后续微蚀不均匀,甚至镀层起泡脱落。
-
需定期更换药液,避免杂质积累影响效果。
-
2. 水洗(Rinsing)
-
目的:彻底清除残留的除油剂,避免交叉污染。
-
方法:
-
采用多级逆流水洗(如DI水),至少2-3道水洗槽,每道水洗时间1-2分钟。
-
-
关键点:
-
水洗不充分会导致微蚀槽污染,缩短药液寿命。
-
监测水质电导率(通常<50 μS/cm),确保清洁度。
-
3. 微蚀(Microetching)
-
目的:轻微腐蚀铜面,增加表面粗糙度,增强镀层结合力;同时去除氧化层。
-
方法:
-
常用药液:过硫酸钠(Na₂S₂O₈)或双氧水-硫酸(H₂O₂-H₂SO₄)体系。
-
微蚀深度控制在0.5-2.0 μm,时间1-2分钟(需根据药液浓度调整)。
-
-
关键点:
-
过蚀会导致铜面粗糙过度,影响线路精度;欠蚀则结合力不足。
-
定期分析微蚀速率(如铜溶解量测试),调整药液浓度。
-
4. 二次水洗
-
目的:去除微蚀后的残留药液及反应产物(如铜离子)。
-
方法:同步骤2,需确保水洗充分。
-
关键点:
-
若残留过硫酸钠,会污染后续酸洗槽,导致铜面钝化。
-
5. 酸洗(Acid Cleaning)
-
目的:活化铜面,去除轻微氧化层,确保铜处于活性状态。
-
方法:
-
使用5-10%稀硫酸(H₂SO₄)浸泡,时间30-60秒。
-
或采用有机酸(如柠檬酸)以降低腐蚀性。
-
-
关键点:
-
酸洗后需彻底水洗,避免硫酸残留影响沉镍液稳定性。
-
铜面若长时间暴露在空气中,需缩短转移时间至沉金槽(<15分钟)。
-
6. 最终水洗与干燥
-
目的:彻底清洁表面,避免污染物带入沉镍金槽。
-
方法:
-
高压喷淋+DI水浸泡,必要时使用热风或氮气干燥。
-
-
关键点:
-
若铜面残留水分,可能稀释沉镍药液,影响反应效率。
-
前处理常见问题与对策
-
镀层结合力差:
-
检查除油和微蚀效果,优化药液浓度及时间。
-
-
铜面氧化:
-
缩短工序间隔时间,酸洗后立即进入沉镍步骤。
-
-
镀层针孔/粗糙:
-
排查水洗是否彻底,微蚀是否均匀。
-
总结
前处理是沉金工艺的基石,需严格控制各步骤参数(浓度、温度、时间)及水洗质量。通过精细化管理,可显著提升镀层均匀性、结合力及产品可靠性,减少后续工艺缺陷。
PCB沉金工艺流程简介预浸
已深度思考(用时 20 秒)
在PCB沉金(ENIG)工艺中,预浸(Pre-dip)是前处理完成后、进入化学镀镍(沉镍)槽前的重要步骤,其主要目的是为后续沉镍反应创造稳定的界面条件,并防止前处理残留液污染沉镍槽。以下是预浸流程的详细介绍及关键控制点:
预浸(Pre-dip)
目的
-
调整铜面状态:
-
中和前处理(如酸洗)后的残留酸性,避免酸性过强直接进入沉镍槽破坏镀液稳定性。
-
在铜表面形成均匀的活化层,促进镍离子的吸附与还原反应。
-
-
保护沉镍槽:
-
清除铜面残留的微量污染物(如氧化物、杂质离子),避免污染沉镍药液。
-
减少镀液中铜离子的带入,延长镀液寿命。
-
方法
-
药液成分:
-
通常为弱酸性溶液(如稀硫酸、柠檬酸或专用预浸剂),pH值控制在2.0-4.0。
-
部分工艺会添加少量络合剂(如EDTA)或表面活性剂,增强活化效果。
-
-
操作参数:
-
温度:常温(25-35℃),无需加热。
-
时间:短时间浸泡,约30-60秒。
-
浓度:根据药液配方调整,例如5-10%稀硫酸或专用预浸剂原液稀释比例。
-
-
流程衔接:
-
预浸后需立即进行水洗(或直接进入沉镍槽,视工艺设计而定)。
-
关键控制点
-
pH值稳定性:
-
预浸液pH需严格监控,避免因酸性过强导致铜面过度腐蚀,或酸性不足导致活化不充分。
-
定期滴定分析药液浓度,及时补充或更换。
-
-
时间控制:
-
预浸时间过短会导致活化不足,沉镍层不均匀;过长可能引入铜溶解风险。
-
-
污染防控:
-
预浸槽需与沉镍槽隔离,避免交叉污染(如预浸液混入沉镍槽会破坏络合剂平衡)。
-
预浸后若需水洗,需使用高纯度DI水(电导率<10 μS/cm)。
-
注意事项
-
药液寿命:
-
预浸液易积累铜离子(来自铜面溶解),需定期更换(通常每班次或每生产100-200 m²板后更换)。
-
-
工艺衔接速度:
-
预浸后需快速转移至沉镍槽(<1分钟),避免铜面二次氧化。
-
-
设备维护:
-
预浸槽材质需耐酸(如PP或PVC),避免金属污染。
-
常见问题与对策
问题 | 可能原因 | 对策 |
---|---|---|
沉镍层结合力差 | 预浸活化不足 | 提高预浸液酸度或延长预浸时间 |
沉镍槽药液快速失效 | 预浸液污染带入沉镍槽 | 加强预浸后水洗或调整隔离设计 |
镀层出现针孔/漏镀 | 预浸后铜面残留氧化物 | 检查预浸液浓度及铜面清洁度 |
总结
预浸是连接前处理与沉镍的核心过渡步骤,通过精准的pH控制与活化处理,可显著提升沉镍层的均匀性和结合力。工艺中需重点关注药液浓度、时间及污染防控,以确保沉金工艺的稳定性和良品率。
免责声明:部分文章信息来源于网络以及网友投稿,本网站只负责对文章进行整理、排版、编辑,意为分享交流传递信息,并不意味着赞同其观点或证实其内容的真实性,如本站文章和转稿涉及版权等问题,请作者在及时联系本站,我们会尽快和您对接处理。
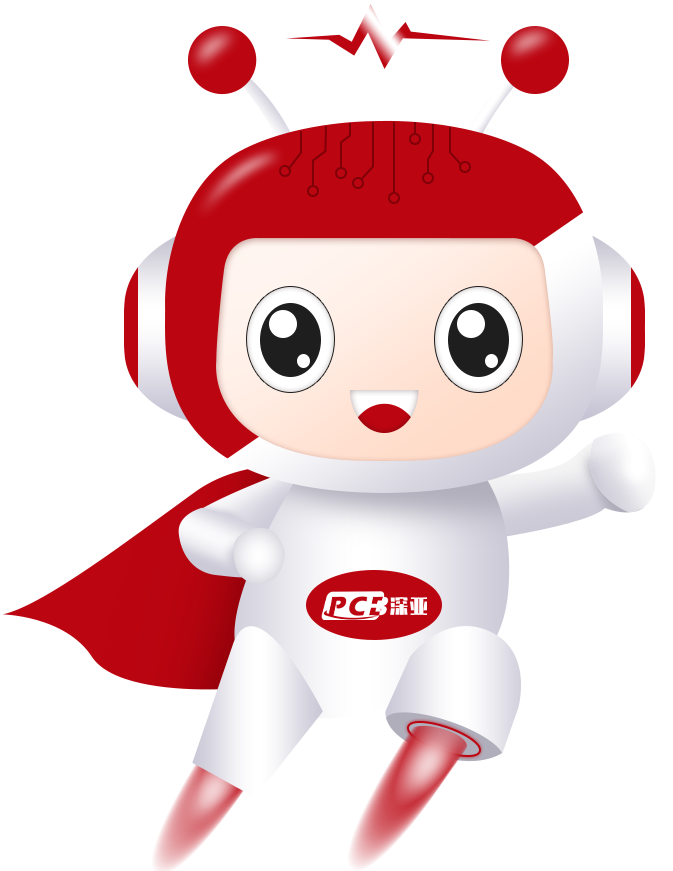